Direct and indirect materials cost
All manufacturing entities essentially use some kind of raw materials to manufacture their output. In a manufacturing environment, the term raw materials refers to the items, matters or substances that are used for manufacturing a salable product. Some of these materials physically become the part of final product while others are just used to carry out the production process and don’t form the product’s physical part or component. The materials that form part of the product are called direct materials whereas the materials that just support and facilitate the process but don’t form part of the product are called indirect materials.
Understanding the basic difference between direct and indirect materials is important in all businesses so that the total product cost and the business profitability can be accurately gauged. Let’s define and explain the two types of materials used in manufacturing processes with the help of some real life examples.
Direct materials cost
Definition and explanation
In relation to manufacturing entities, the term direct materials signifies one or more items, matters or substances that are either physically transformed into a useable product or that become part or component of that product. The cost of such materials is directly traceable to each individual unit of product manufactured and is, therefore, regarded as direct or product cost. The quantity of direct materials needed to make a unit of product is usually known or can be closely estimated. For example, an engineer working in a furniture manufacturing company can easily tell you the quantity of wood, glue, nails and length of glass sheet needed to manufacture an executive table. The direct materials often form a major element of total prime cost of a given manufacturing process.
The quantity of direct materials needed to complete a unit of product is determined by the “bill of materials”. It is a well organized document which is prepared by combined effort of engineering and production department. The document contains information regarding all the items, materials and components along with their right quantities needed to manufacture a complete and shippable product. It also provides the basic work instructions and notes. Once prepared, the bill of materials authorizes the production manager to request materials from storage department.
Direct materials are requested from storage department using “materials requisition form”. This form is filled and signed by the production manager and sent to the materials manager who, after performing a formal verification, approves the requisition. The each material in requested quantity is then released and moved from the storage to production area.
For balance sheet purpose, the direct materials is classified as current asset and is reported at its cost. The cost of direct materials purchased consists of price paid to supplier (including sales taxes) plus duties and shipment cost. The quantity of materials left unused in the stock at the end of an accounting period is presented in balance sheet as a line item named “Raw Materials Inventory”.
The entities need to properly track their purchase and consumption of direct materials so that they can avoid shortage or unnecessary stock keeping. Shortage of materials may disrupt production as well as cause additional ordering cost to the entity while unnecessary or excessive inventory in stock may lead to materials obsolescence loss.
Examples of direct materials
Nature is probably the biggest source of industrial inputs. Various types of direct materials that are consumed in different manufacturing industries usually come from natural deposits, agricultural fields, forests and animals etc. However, the situations are not uncommon where the output of one business is further processed by another business to create a final and useable product.
A few examples of direct materials used in different industries are given below:
- Wood, fabric, nails and glue used by furniture manufacturing businesses like Herman Miller, HNI, TJX and Ashley.
- Leather used by a shoe manufacturing company like Bata, Service and Hash Puppy.
- Limestone, marl, clay, shale used by cement producers like Cemex, Lehigh Hanson, Ash Grove and Buzzi Unicem.
- Natural gas and anhydrous ammonia used by the producers of urea fertilizer like Agree Life, Reap Chemicals and Prime Agro.
- Flour, milk, grain, egg, butter, cheese, honey, fruit pulp, sugar, salt, spices and vegetable oil used by snack and baking companies like Mondelez International, B&G, Treehouse, Conagra and Hain Celestial Group.
- Steel and tyres used by automobile manufacturers like Mercedes, Honda, Toyota, Hino and Tata Motors.
- Rubber used by tyres manufacturing companies like Yokohama, Continental, Goodyear and Hankook.
- Plastic used by toy manufacturing companies like Hasbro, Funko, Lego and Imperial Toys.
- Cotton and silk used by producers of fabric and carpets like InPro, Fabrico, Unifi, Albani International.
- Sugar beets and sugarcane used by sugar producing companies like American Crystal, Michigan Sugar and C&H Sugar Company.
We can observe that, in many situations, the finished product of one business is used as direct materials by another business. An example of such a situation can be found in construction industry where the cement is used by house and apartment construction companies. Cement is the finished product of cement manufacturers but is used as direct material by construction companies. Car manufacturing companies are another example of such situations. Mercedes Benz, for instance, purchases tyres from Yokohama. Tyres are the finished product of Yokohama but direct material for Mercedes Benz that uses them to complete manufacturing of its cars and other automobiles.
Direct materials have the following relations with terms product cost, inventoriable cost, manufacturing cost and prime cost:
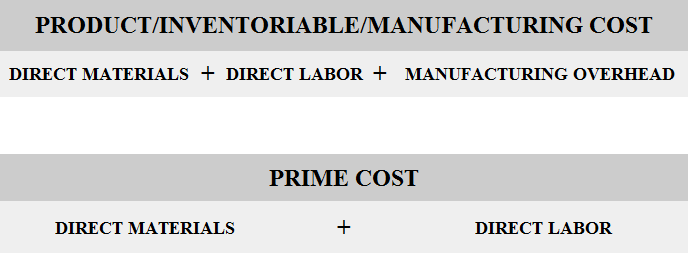
Indirect materials cost
Definition and explanation
The term indirect materials refers to one or more items, matters or substances that are essential to carry out a production or manufacturing process but they don’t physically become the part of product or a component of it. The cost of such materials is classified as indirect cost because it can’t be easily and conveniently traced, linked or associated to a unit of product or a job order.
The procedure for drawing indirect materials from storage is similar to the direct materials i.e., they are requested by production manager via a materials requisition form.
The cost of indirect materials used is added to the entity’s manufacturing overhead cost and, thus, ultimately made part of the total product cost. However, if the amount is significantly minor, the cost of these materials can be directly charged to expense as incurred during a period. The selection from the either approach is largely impacted by the entity’s costing policies.
Examples of indirect materials
Some common examples of items treated as indirect materials in manufacturing businesses are listed below:
- The cost of oil and grease used to lubricate moving parts of machines used in a manufacturing operation.
- Air and oil filters used in machines, furnaces and ventilation systems.
- Protective equipment like gloves, glasses, eyewear and hamlets etc. used by factory workers.
- disposable/expendable tools and safety equipment.
- Adhesives, glues and tapes.
- Supplies used for washing and cleaning purposes.
- Fittings and fasteners.
- Use of pins, gums, staples, pencils etc. in a service providing firm.
Important points to remember:
The six points listed below may be helpful for students to summarize and learn the basic difference between direct and indirect materials:
- Direct materials are tangible items and ingredients which are physically included in a product and which can be easily identified with that product. Examples include timber for manufacturing a chair, steal for a car and orange pulp to produce orange jam.
- Indirect materials are essential for production operations but they are not physically added to the product and also they can’t be easily and conveniently linked to or identified with a particular product. Examples include oil filters, air filters, grease and disposable items like gloves used in a manufacturing process.
- Both direct and indirect materials are essentially part of the product cost, also called manufacturing cost or inventoriable cost.
- The type and quantity of both the materials needed to complete a unit of final product is specified by bill of materials – a document prepared by engineering and production department.
- To start or continue manufacturing process, production manager uses materials requisition form to request the required quantity of materials from storage department.
- Indirect materials cost is often added to the manufacturing overhead and therefore automatically becomes the part of entity’s manufacturing or product cost. If, however, the amount is insignificant, the entity can opt to expense such cost as incurred. The cost of materials so treated don’t contribute to manufacturing or product cost but are charged to profit and loss account or income statement in its entirety like other period costs.
Leave a comment